05 Apr How gas leaks are detected at MTU Maintenance Berlin-Brandenburg
Leak Detection within Turbine Enclosures
How gas leaks are detected at MTU Maintenance
Berlin-Brandenburg
A leak in a line for compressed air, steam, CO2, CH4 or H2 does not only represent a financial risk, but also poses a threat to life and limb. For example, a leak in a gas turbine enclosure can pose a significant health and safety risk to workers. On oil rigs, leaks can even result in fire.
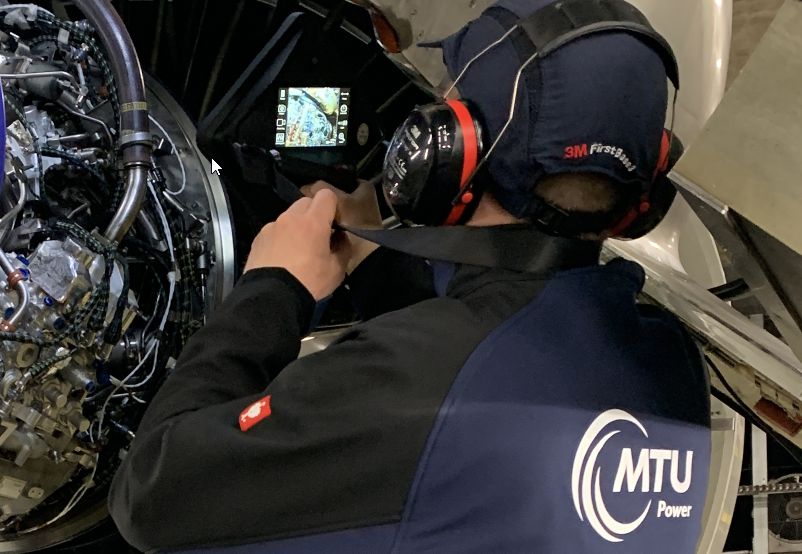
Leak Detection within Turbine Enclosures
How gas leaks are detected at MTU Maintenance Berlin-Brandenburg
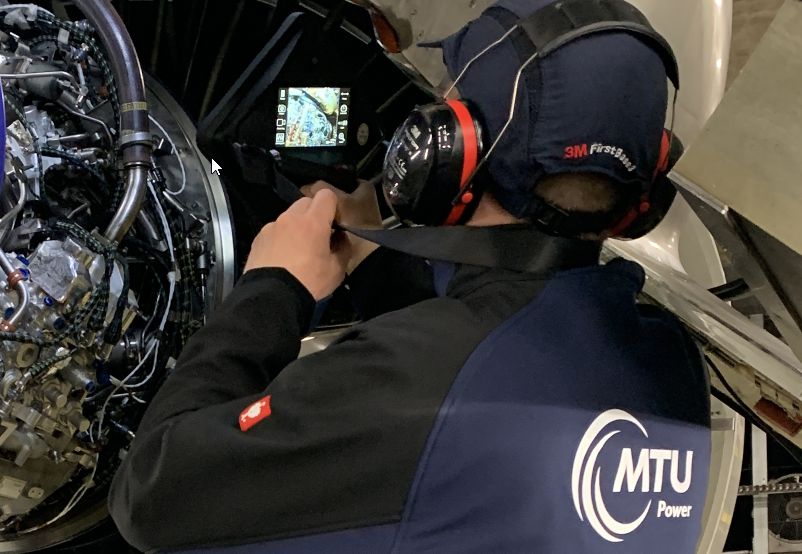
A leak in a line for compressed air, steam, CO2, CH4 or H2 does not only represent a financial risk, but also poses a threat to life and limb. For example, a leak in a gas turbine enclosure can pose a significant health and safety risk to workers. On oil rigs, leaks can even result in fire.
“We enhance occupational safety and minimize the risk of unplanned downtime”
The Distran Ultra Pro acoustic camera displays the exact leak location and estimates the leakage rate in real time. Indeed, the technology is able to detect ultrasound waves emitted by gas flow as it rushes out small holes, seams and cracks. The acoustic information is overlaid on an optical image in real time, enabling a clear pinpointing of leaks.
Traditional leak detection methods commonly used in factories, such as soap spray, lasers or quite simple hand-held detectors (‘sniffers’), could be applied relatively easily. Unfortunately, they do not always bring the desired results, as Matthias Witt, Director IGT Field Service & Package at MTU Maintenance Berlin-Brandenburg in Ludwigsfelde explains.
The Field Service in Ludwigsfelde inspects gas turbines for leaks in the fuel supply system following modifications or maintenance. “Such leaks are sometimes very difficult to locate and lead to unplanned downtime as well as risks in operating the plant. Leaking connecting elements on the compressor or seal air systems can lead to machine damage in the long term. Damaged, i.e. leaking, expansion joints and connecting elements in the air system as well as in the exhaust tract lead to unplanned downtime and thus to plant failure.”
“We enhance occupational safety and minimize the risk of unplanned downtime”
The Distran Ultra Pro acoustic camera displays the exact leak location and estimates the leakage rate in real time. Indeed, the technology is able to detect ultrasound waves emitted by gas flow as it rushes out small holes, seams and cracks. The acoustic information is overlaid on an optical image in real time, enabling a clear pinpointing of leaks.
Traditional leak detection methods commonly used in factories, such as soap spray, lasers or quite simple hand-held detectors (‘sniffers’), could be applied relatively easily. Unfortunately, they do not always bring the desired results, as Matthias Witt, Director IGT Field Service & Package at MTU Maintenance Berlin-Brandenburg in Ludwigsfelde explains.
The Field Service in Ludwigsfelde inspects gas turbines for leaks in the fuel supply system following modifications or maintenance. “Such leaks are sometimes very difficult to locate and lead to unplanned downtime as well as risks in operating the plant. Leaking connecting elements on the compressor or seal air systems can lead to machine damage in the long term. Damaged, i.e. leaking, expansion joints and connecting elements in the air system as well as in the exhaust tract lead to unplanned downtime and thus to plant failure.”
Matthias Witt heard about the use of Distran’s ultrasound camera on the International Space Station by the NASA, and started a test phase with the device: “We mainly want to use the detector for standardized leakage check-ups after recommissioning of the gas turbines. This way, we enhance occupational safety and minimize the risk of unplanned downtime,” he explains.
With his team, he tested the system in a test cell for industrial gas turbines. “The air leaks we simulated were detected very quickly, even when the test cell was highly ventilated.” Further tests in commercially operated plants followed. “Leaks could be located from a safe distance – a real benefit in terms of occupational safety,” says Matthias Witt. Since the system is portable, it is now also used for worldwide service assignments and in R&D projects. “It could even be used on aircraft engines, an application we are currently assessing in the relevant group divisions.”
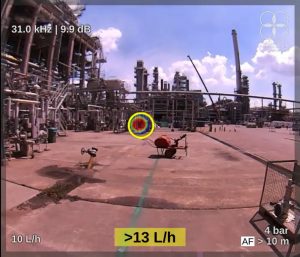
The ultrasound camera pinpoints the leaks from a distance.
Leak indication and leak rate estimation are displayed in real-time on the device’s screen.
Matthias Witt heard about the use of Distran’s ultrasound camera on the International Space Station by the NASA, and started a test phase with the device: “We mainly want to use the detector for standardized leakage check-ups after recommissioning of the gas turbines. This way, we enhance occupational safety and minimize the risk of unplanned downtime,” he explains.
With his team, he tested the system in a test cell for industrial gas turbines. “The air leaks we simulated were detected very quickly, even when the test cell was highly ventilated.” Further tests in commercially operated plants followed. “Leaks could be located from a safe distance – a real benefit in terms of occupational safety,” says Matthias Witt. Since the system is portable, it is now also used for worldwide service assignments and in R&D projects. “It could even be used on aircraft engines, an application we are currently assessing in the relevant group divisions.”
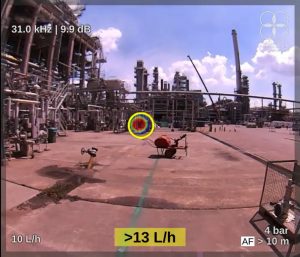
The ultrasound camera pinpoints the leaks from a distance.
Leak indication and leak rate estimation are displayed in real-time on the device’s screen.
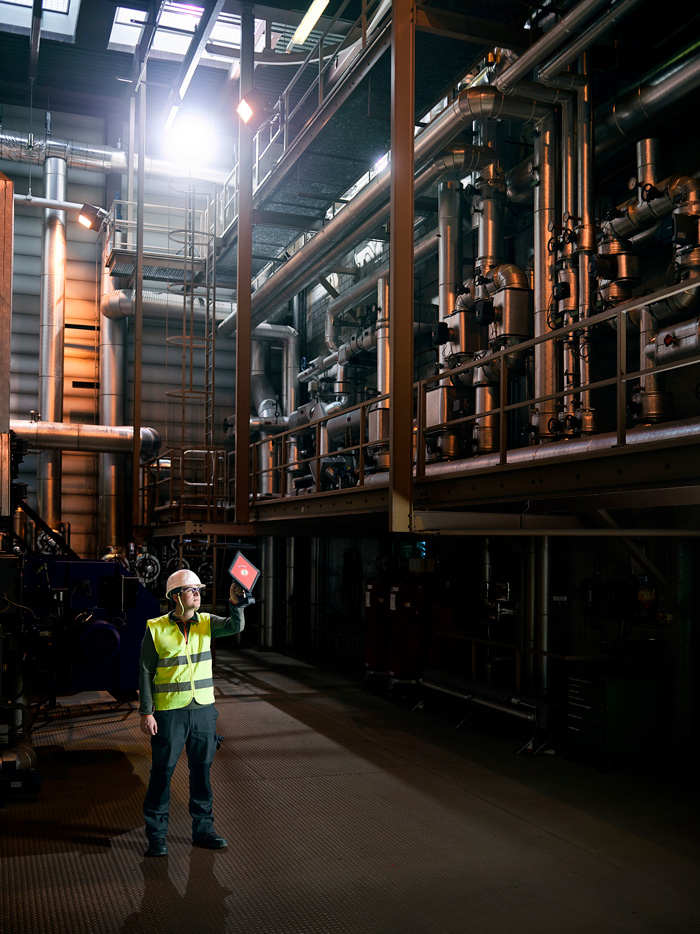
Florian Höchli, DACH Sales Manager at manufacturer Distran, explains how the ultrasound camera works: “As we know, gas leaks emit ultrasounds. The Acoustic Leak Imaging (ALI) technique used by the device detects these acoustic emissions.” An ultrasound camera consists of an array of ultrasound microphones, which are mounted on a 2D panel together with an optical camera. When an ultrasound wave hits this panel, it reaches each microphone at a different time. These differences are used by the camera to locate the ultrasound source. The acoustic leak information is instantly superimposed on the image captured by the optical camera and visually displayed on the built-in screen, so that the user can literally see the leaks.
This technology is relatively new: The first ultrasound camera was developed in 2013 in collaboration with Alstom (later General Electric) to inspect power plants. Distran’s technology is used in different types of thermal power plants: gas and steam power plants, coal-fired power plants, aeroderivative gas turbine power plants, waste-fueled power plants and nuclear power plants.
Florian Höchli, DACH Sales Manager at manufacturer Distran, explains how the ultrasound camera works: “As we know, gas leaks emit ultrasounds. The Acoustic Leak Imaging (ALI) technique used by the device detects these acoustic emissions.” An ultrasound camera consists of an array of ultrasound microphones, which are mounted on a 2D panel together with an optical camera. When an ultrasound wave hits this panel, it reaches each microphone at a different time. These differences are used by the camera to locate the ultrasound source. The acoustic leak information is instantly superimposed on the image captured by the optical camera and visually displayed on the built-in screen, so that the user can literally see the leaks.
This technology is relatively new: The first ultrasound camera was developed in 2013 in collaboration with Alstom (later General Electric) to inspect power plants. Distran’s technology is used in different types of thermal power plants: gas and steam power plants, coal-fired power plants, aeroderivative gas turbine power plants, waste-fueled power plants and nuclear power plants.
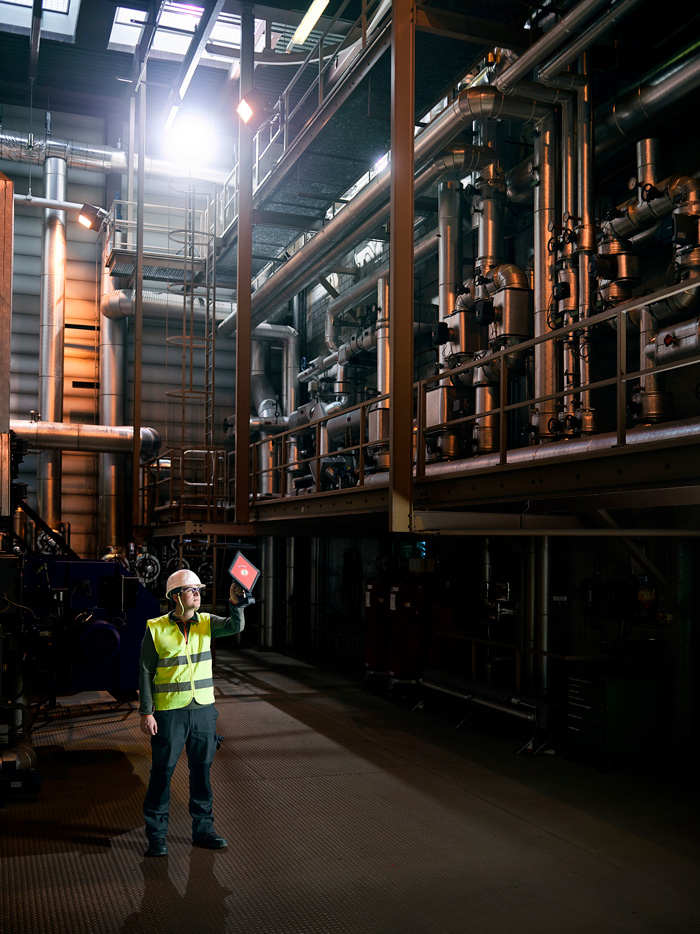
“Due to the many different gas systems used (methane, steam, compressed air and vacuum) and the very high reliability and availability requirements of the plants, the ultrasound cameras are used particularly in gas and steam turbine power plants,” says Florian Höchli.
The young company is not afraid of big names: “Among our customers are leading industrial companies such as General Electric, Air Liquide, Shell, TotalEnergies, RWE and BASF.” And – as the highest ranking example, so to speak – the astronauts of the ISS.
“Due to the many different gas systems used (methane, steam, compressed air and vacuum) and the very high reliability and availability requirements of the plants, the ultrasound cameras are used particularly in gas and steam turbine power plants,” says Florian Höchli.
The young company is not afraid of big names: “Among our customers are leading industrial companies such as General Electric, Air Liquide, Shell, TotalEnergies, RWE and BASF.” And – as the highest ranking example, so to speak – the astronauts of the ISS.