06 Avr Turbines à gaz : détection des fuites chez MTU Maintenance
Détection de fuites sur les turbines à gaz
Comment les fuites de gaz sont détectées chez MTU Maintenance Berlin-Brandenburg
Une fuite dans une conduite d’air comprimé, de vapeur, de CO2, de CH4 ou de H2 ne représente pas seulement un risque financier, mais constitue également une menace pour la sécurité. Par exemple, une fuite dans l’enceinte d’une turbine à gaz peut représenter un risque important pour la santé et la sécurité du personnel de terrain. Sur les plates-formes pétrolières, les fuites peuvent aussi provoquer de graves incendies.
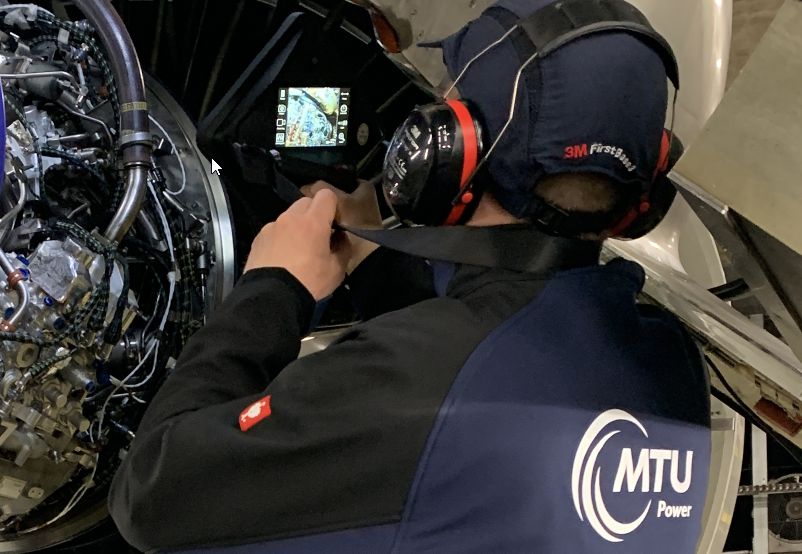
Détection de fuites de gaz dans les enceintes de turbines
Comment les fuites de gaz sont détectées chez MTU Maintenance Berlin-Brandenburg
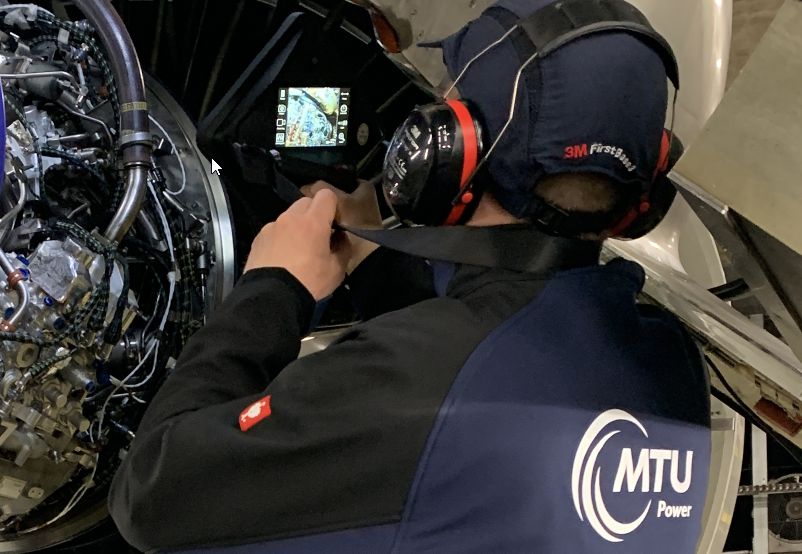
Une fuite dans une conduite d’air comprimé, de vapeur, de CO2, de CH4 ou de H2 ne représente pas seulement un risque financier, mais constitue également une menace pour la sécurité. Par exemple, une fuite dans l’enceinte d’une turbine à gaz peut représenter un risque important pour la santé et la sécurité du personnel de terrain. Sur les plates-formes pétrolières, les fuites peuvent aussi provoquer de graves incendies.
“Nous améliorons la sécurité et minimisons le risque d’arrêts non planifiés”
La caméra ultrasons Ultra Pro de Distran indique l’emplacement des fuites de gaz et estime leur taux de fuite en temps réel. En effet, la technologie est capable de détecter les ondes ultrasonores émises par le flux de gaz alors qu’il s’échappe par des trous, joints ou fissures. L’information acoustique ainsi obtenue est superposée en temps réel à une image optique, permettant de localiser clairement les fuites.
Les méthodes traditionnelles de détection de fuites utilisées dans les environnements industriels, tels que le mille-bulles, le lasers ou le « sniffeur » pourraient être déployés facilement. Cependant, elles n’apportent pas toujours les résultats escomptés, comme l’explique Matthias Witt, directeur IGT Field Service & Package chez MTU Maintenance Berlin-Brandenburg à Ludwigsfelde.
Lors de modifications ou lors d’opérations de maintenance, les opérateurs de MTU inspectent les turbines à gaz à la recherche de fuites dans le système d’alimentation en carburant. « Ces fuites sont parfois très difficiles à localiser et entraînent des temps d’arrêts non planifiés, ainsi que des risques importants dans l’exploitation de la centrale. Des éléments de raccordement non étanches sur le compresseur ou sur les systèmes d’étanchéité peuvent également entraîner des dommages à long terme. Des joints de dilatation ou des éléments de raccordement non étanches, dans le système d’air ainsi que dans le conduit d’échappement, entraînent des temps d’arrêts non planifiés et donc une défaillance complète de l’installation ».
“Nous améliorons la sécurité et minimisons le risque d’arrêts non planifiés”
La caméra ultrasons Ultra Pro de Distran indique l’emplacement des fuites de gaz et estime leur taux de fuite en temps réel. En effet, la technologie est capable de détecter les ondes ultrasonores émises par le flux de gaz alors qu’il s’échappe par des trous, joints ou fissures. L’information acoustique ainsi obtenue est superposée en temps réel à une image optique, permettant de localiser clairement les fuites.
Les méthodes traditionnelles de détection de fuites utilisées dans les environnements industriels, tels que le mille-bulles, le lasers ou le « sniffeur » pourraient être déployés facilement. Cependant, elles n’apportent pas toujours les résultats escomptés, comme l’explique Matthias Witt, directeur IGT Field Service & Package chez MTU Maintenance Berlin-Brandenburg à Ludwigsfelde.
Lors de modifications ou lors d’opérations de maintenance, les opérateurs de MTU inspectent les turbines à gaz à la recherche de fuites dans le système d’alimentation en carburant. « Ces fuites sont parfois très difficiles à localiser et entraînent des temps d’arrêts non planifiés, ainsi que des risques importants dans l’exploitation de la centrale. Des éléments de raccordement non étanches sur le compresseur ou sur les systèmes d’étanchéité peuvent également entraîner des dommages à long terme. Des joints de dilatation ou des éléments de raccordement non étanches, dans le système d’air ainsi que dans le conduit d’échappement, entraînent des temps d’arrêts non planifiés et donc une défaillance complète de l’installation ».
Matthias Witt a entendu parler du déploiement de la caméra ultrasons de Distran par la NASA à bord de la Station Spatiale Internationale à la recherche de fuites d’air et a démarré une phase de test de cet outil : « Nous souhaitons principalement utiliser cette caméra pour des contrôles d’étanchéité après la remise en service des turbines à gaz. Ainsi, nous améliorons la sécurité au travail et minimisons le risque de temps d’arrêt non planifié », explique-t-il.
Avec son équipe, il a testé le système Distran dans une cellule d’essai pour turbines à gaz industrielles. « Les fuites d’air que nous avions simulées ont été détectées très rapidement, même lorsque la cellule d’essai était fortement ventilée ». D’autres tests ont ensuite été réalisés au sein d’installations en fonctionnement. « Les fuites ont été localisées à une distance de sécurité ; un réel avantage en termes de sécurité au travail », explique Matthias Witt. Puisque le système est portatif, il est désormais utilisé pour des missions de service dans le monde entier et dans nos projets de R&D. « Il pourrait même être utilisé sur les moteurs d’avion, une application que nous sommes en train d’évaluer dans les divisions concernées du groupe ».
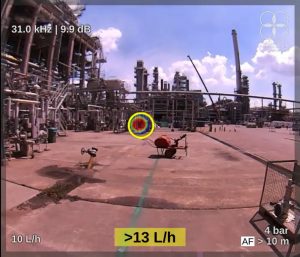
La caméra ultrasons détecte et localise les fuites à distance.
L’emplacement des fuites et l’estimation du taux de fuite s’affichent en temps réel à l’écran.
Matthias Witt a entendu parler du déploiement de la caméra ultrasons de Distran par la NASA à bord de la Station Spatiale Internationale à la recherche de fuites d’air et a démarré une phase de test de cet outil : « Nous souhaitons principalement utiliser cette caméra pour des contrôles d’étanchéité après la remise en service des turbines à gaz. Ainsi, nous améliorons la sécurité au travail et minimisons le risque de temps d’arrêt non planifié », explique-t-il.
Avec son équipe, il a testé le système Distran dans une cellule d’essai pour turbines à gaz industrielles. « Les fuites d’air que nous avions simulées ont été détectées très rapidement, même lorsque la cellule d’essai était fortement ventilée ». D’autres tests ont ensuite été réalisés au sein d’installations en fonctionnement. « Les fuites ont été localisées à une distance de sécurité ; un réel avantage en termes de sécurité au travail », explique Matthias Witt. Puisque le système est portatif, il est désormais utilisé pour des missions de service dans le monde entier et dans nos projets de R&D. « Il pourrait même être utilisé sur les moteurs d’avion, une application que nous sommes en train d’évaluer dans les divisions concernées du groupe ».
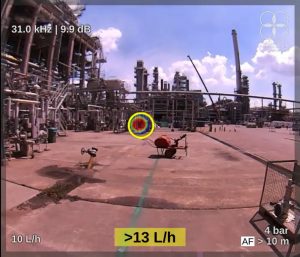
La caméra ultrasons détecte et localise les fuites à distance.
L’emplacement des fuites et l’estimation du taux de fuite s’affichent en temps réel à l’écran.
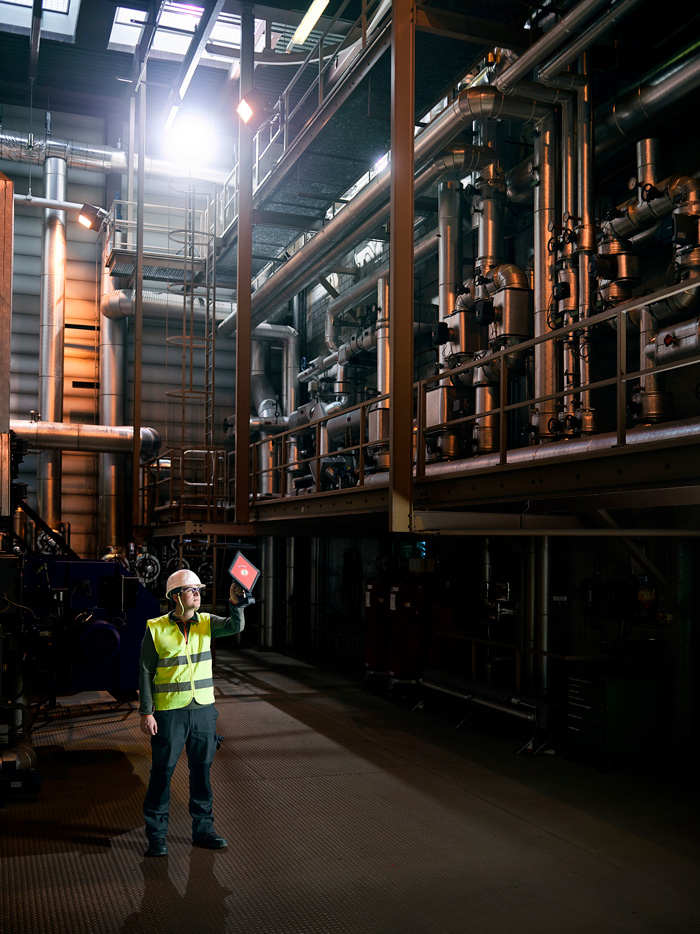
Florian Höchli, DACH Sales Manager chez Distran, explique le fonctionnement de la caméra à ultrasons : « Comme nous le savons, les fuites de gaz émettent des ultrasons. La technologie de la caméra Distran : Acoustic Leak Imaging (ALI) permet de détecter ces émissions acoustiques ». Une caméra à ultrasons se compose d’un réseau de microphones à ultrasons, montés sur un panneau avec une caméra optique. Lorsqu’une onde ultrasonore frappe ce panneau, elle atteint chaque microphone à un moment différent. Ces micro différences de temps sont utilisées par la caméra pour localiser la source des ultrasons. Les informations acoustiques relevées sont instantanément superposées à l’image capturée par la caméra optique et sont affichées sur l’écran, de sorte que l’utilisateur puisse littéralement voir les fuites.
Cette technologie est relativement récente : la première caméra à ultrasons a été développée en 2013 en collaboration avec Alstom (devenu General Electric) pour inspecter les centrales électriques. La technologie de Distran est déployée dans différents types de centrales thermiques : centrales à gaz et à vapeur, centrales à charbon, turbine à gaz, centrales à déchets et centrales nucléaires.
Florian Höchli, DACH Sales Manager chez Distran, explique le fonctionnement de la caméra à ultrasons : « Comme nous le savons, les fuites de gaz émettent des ultrasons. La technologie de la caméra Distran : Acoustic Leak Imaging (ALI) permet de détecter ces émissions acoustiques ». Une caméra à ultrasons se compose d’un réseau de microphones à ultrasons, montés sur un panneau avec une caméra optique. Lorsqu’une onde ultrasonore frappe ce panneau, elle atteint chaque microphone à un moment différent. Ces micro différences de temps sont utilisées par la caméra pour localiser la source des ultrasons. Les informations acoustiques relevées sont instantanément superposées à l’image capturée par la caméra optique et sont affichées sur l’écran, de sorte que l’utilisateur puisse littéralement voir les fuites.
Cette technologie est relativement récente : la première caméra à ultrasons a été développée en 2013 en collaboration avec Alstom (devenu General Electric) pour inspecter les centrales électriques. La technologie de Distran est déployée dans différents types de centrales thermiques : centrales à gaz et à vapeur, centrales à charbon, turbine à gaz, centrales à déchets et centrales nucléaires.
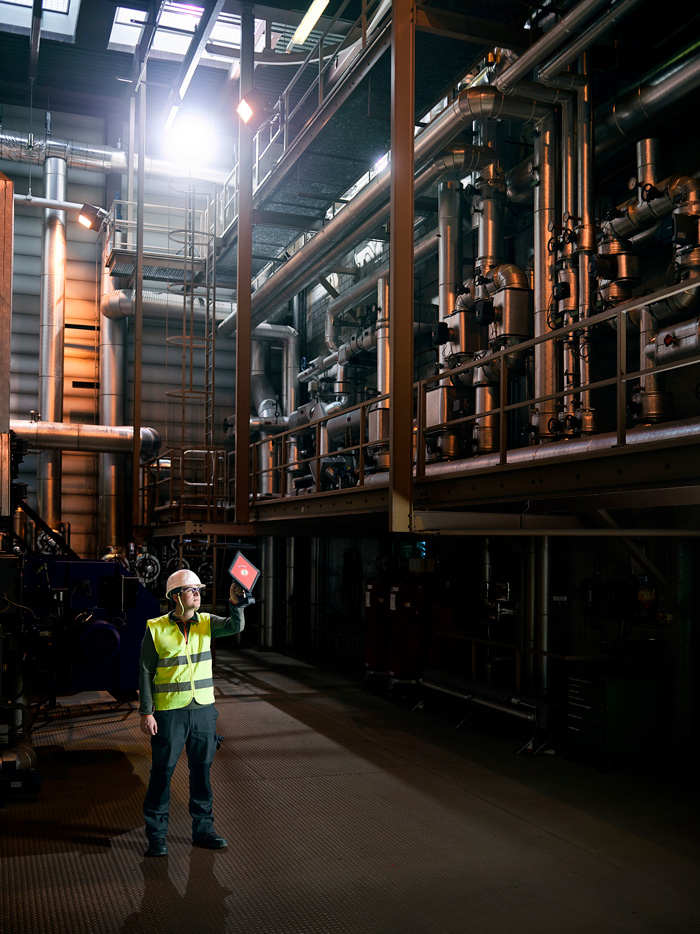
« En raison de la variété de systèmes de gaz utilisés (méthane, vapeur, air comprimé et vide) et des exigences très élevées en matière de fiabilité et de disponibilité des installations industrielles, les caméras ultrasons sont particulièrement utilisées dans les centrales à turbine à gaz et à vapeur », explique Florian Höchli.
La jeune entreprise n’a pas peur des grands noms : « Parmi nos clients figurent des entreprises industrielles de premier plan telles que General Electric, Air Liquide, Shell, TotalEnergies, EDF, RWE et BASF ». Sans oublier les astronautes à bord de l’ISS.
« En raison de la variété de systèmes de gaz utilisés (méthane, vapeur, air comprimé et vide) et des exigences très élevées en matière de fiabilité et de disponibilité des installations industrielles, les caméras ultrasons sont particulièrement utilisées dans les centrales à turbine à gaz et à vapeur », explique Florian Höchli.
La jeune entreprise n’a pas peur des grands noms : « Parmi nos clients figurent des entreprises industrielles de premier plan telles que General Electric, Air Liquide, Shell, TotalEnergies, EDF, RWE et BASF ». Sans oublier les astronautes à bord de l’ISS.