21 Dec Nuclear power generation: ensuring the availability of the Dampierre-en-Burly plant
Dampierre-en-Burly Nuclear Power Plant success story
Nuclear power generation: ensuring the availability of the Dampierre-en-Burly plant
Key facts:
EDF Dampierre-en-Burly has been detecting leaks of all gas types, including hydrogen, compressed air, steam, and air ingress, with the Distran Ultra Pro since 2021.
Distran’s leak rate quantification feature helped EDF avert a shutdown that would have cost 5 to 6 million euros per day.
Today, the teams in charge use the Distran device and the integrated reporting tool to monitor equipment over time ensuring the plant’s availability.
Dampierre-en-Burly Nuclear Power Plant customer success story
Nuclear power generation: guaranteeing the availability of the Dampierre-en-Burly plant
Key facts:
EDF Dampierre-en-Burly has been detecting leaks of all gas types, including hydrogen, compressed air, steam, and air ingress, with the Distran Ultra Pro since 2021.
Distran’s leak rate quantification feature helped EDF avert a shutdown that would have cost 5 to 6 million euros per day.
Today, the teams in charge use the Distran device and the integrated reporting tool to monitor equipment over time ensuring the plant’s availability.
EDF‘s nuclear power plant in Dampierre-en-Burly, produces ~20 TWh of low-CO2-emitting electricity per year (around 8% of France’s nuclear electricity production), equivalent to the electricity consumption of 4 million homes.
At a nuclear power plant, safety is key. That’s why, the early detection of any equipment malfunction is paramount to guaranteeing the availability of such facilities.
Searching for and repairing leaks of compressed air, steam, and vacuum (air ingress), as well as various other gases, are among the preventive operations carried out. The teams in charge have been using the Distran ultrasound camera since 2021.
“The Distran ultrasonic camera has proved to be an invaluable tool,
helping us to monitor numerous pieces of equipment.
Such as our production system of control air (SAR),
ventilation systems (HVAC), or to monitor our condenser, kept at a negative pressure.
And, to ensure proper operation of equipment, such as the ones monitoring the radioactivity in the environment,
called KRT chain.”
Xavier Bacquenois
Plant Manager – EDF NPP Dampierre-en-Burly
Tense energy context: no compromise on safety and security
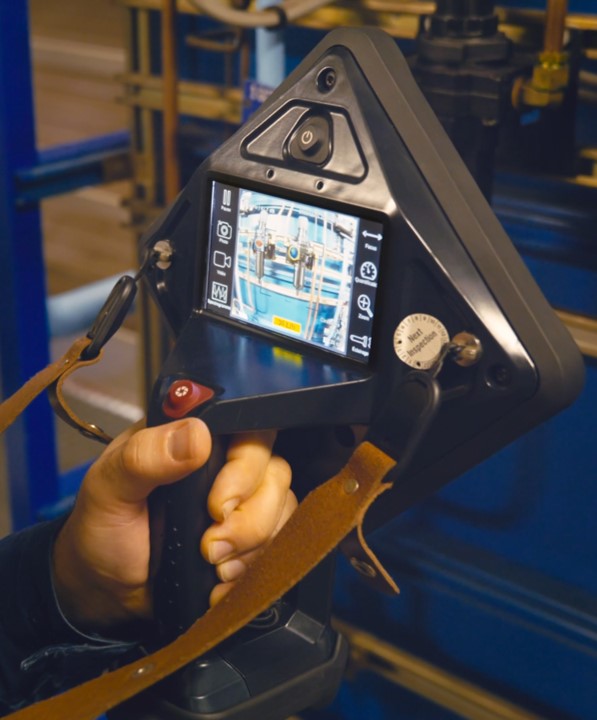
In January 2023, the French electricity production network was excessively strained, in particular as a result of the stress corrosion cracking encountered on French nuclear plants. At the time, it was vital to guarantee the availability of the Dampierre-en-Burly facilities. Then, an air leak was detected on a valve of the turbine bypass system (called “GCTa” in French) as part of a periodic test campaign.
A leak on this equipment triggers a so-called group 1 event. This means:
- In accordance with the safety regulations, the teams in charge have 8 hours to determine the damages and ensure that it has no impact on safety.
- If failed, the unit must be shut down to start maintenance operations.
- To avoid a shutdown, the teams must be able to quantify the leak, monitor it over time, and ensure that it remains below the safety thresholds.
The leak was initially detected with soap spray, method which do not provide leak rate quantification. The alternative methods regularly deployed at Dampierre-en-Burly are proven techniques, such as a smoke machine or acoustic monitoring.
However, these are complex technologies and do not provide conclusive results in such a short timeframe.
Leaks detected within French Nuclear Power Plant fleet using using Distran Ultra Pro X
Air leak on valve
Turbine bypass system (GCTa)
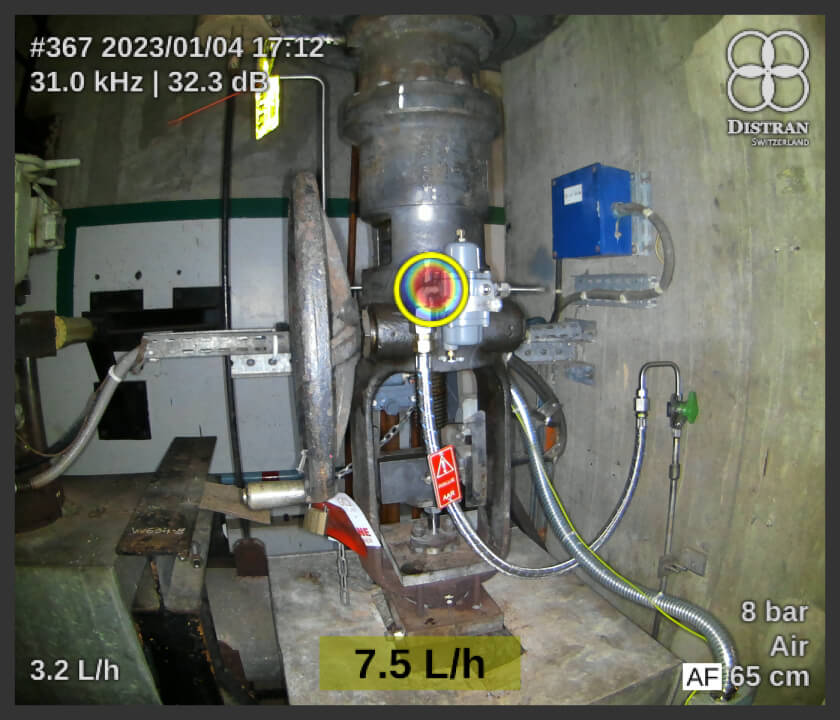
Steam leak on valve
Turbine bypass system (GCTc)
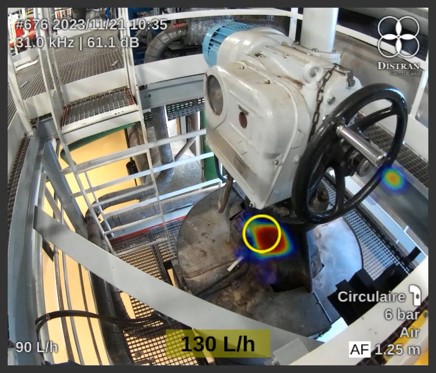
Air ingress
Steam turbine housing
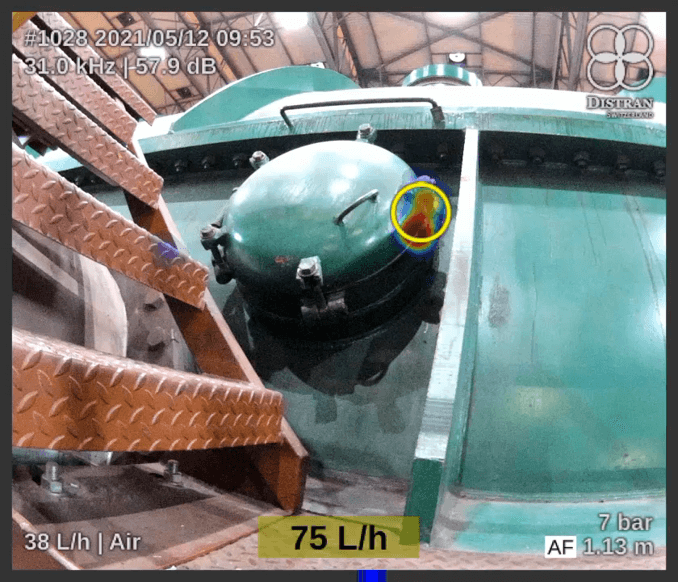
Rapid response:
EDF takes advantage of swift leak rate quantification
Due to the time pressure, the teams in charge counted on the Distran acoustic camera to take on the challenge:
- The Ultra Pro enabled the staff to quantify the leak rate and set up the monitoring over time in under 1 hour.
- Once the leak rate had been quantified and determined to be well below the regulatory thresholds, the production management team decided to continue.
- In addition, long-term monitoring was put in place. To date, the size of the leak has not exceeded the regulatory threshold.
Later during the year, operators detected another leak on the same equipment. Again, the responsible staff could measure the leak rate quickly with the Distran device and execute appropriate repair activities to continue production.
Distran’s integrated reporting tool Audalytics includes leak rates, photos, and videos captured with Ultra Pro to create inspection reports in a few clicks. This feature is very useful for comparing the collected data and monitoring the evolution of leaks over time, which is a central element of asset management and maintenance.
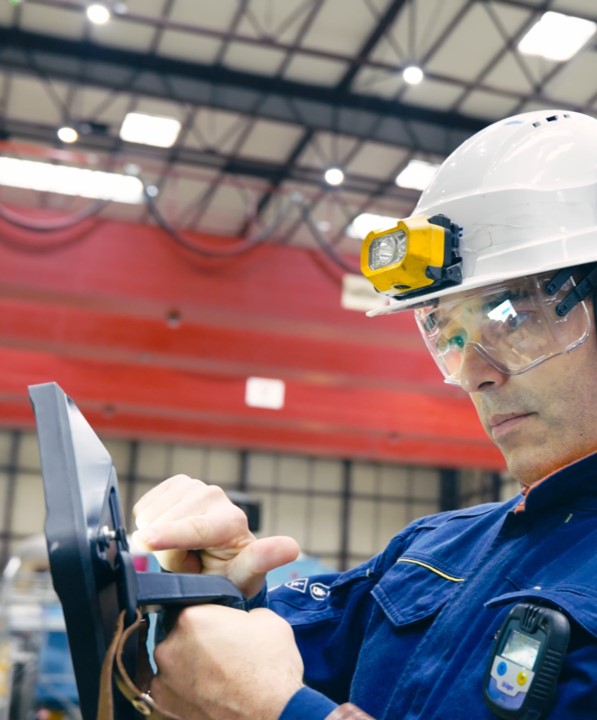
Rapid response: EDF takes advantage of swift leak rate quantification
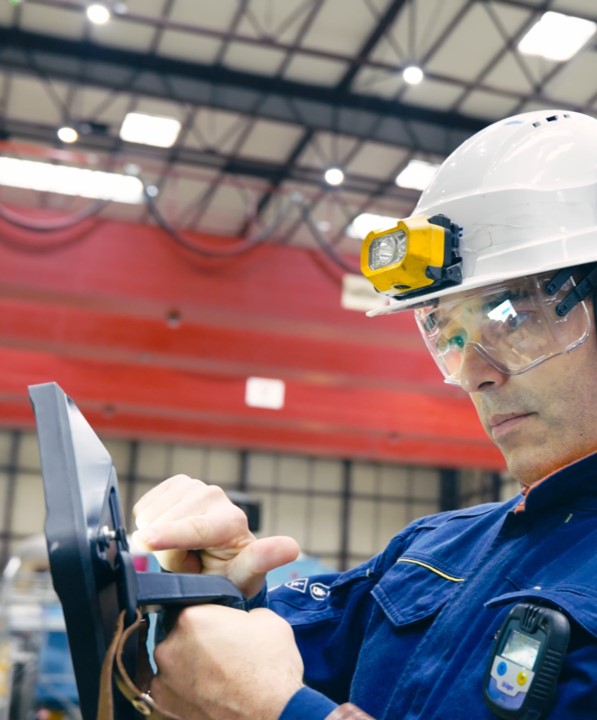
Due to the time pressure, the teams in charge counted on the Distran acoustic camera to take on the challenge:
- The Ultra Pro enabled the staff to quantify the leak rate and set up the monitoring over time in under 1 hour.
- Once the leak rate had been quantified and determined to be well below the regulatory thresholds, the production management team decided to continue.
- In addition, long-term monitoring was put in place. To date, the size of the leak has not exceeded the regulatory threshold.
Later during the year, operators detected another leak on the same equipment. Again, the responsible staff could measure the leak rate quickly with the Distran device and execute appropriate repair activities to continue production.
Distran’s integrated reporting tool Audalytics includes leak rates, photos, and videos captured with Ultra Pro to create inspection reports in a few clicks. This feature is very useful for comparing the collected data and monitoring the evolution of leaks over time, which is a central element of asset management and maintenance.
How Distran Ultra Pro ultrasound cameras support Nuclear Power Plants:

ENSURE HIGH AVAILABILITY

GUARANTEE NUCLEAR SAFETY

SAFEGUARD HUMAN SAFETY
“The unique features of the Distran acoustic camera, in particular the quantification of the leak rate,
empowered us to estimate the degree of urgency for intervention.
In addition to ensuring continuity of supply to the network, the avoided shutdown
would have cost between 5 to 6 million euros per day of shutdown.”
Xavier Bacquenois
Plant Manager – EDF NPP Dampierre-en-Burly
Diagnostics and monitoring: safeguarding the availability of France’s nuclear power plants fleet
As for all French nuclear power plants, EDF’s paramount objective in Dampierre-en-Burly is to produce low-carbon electricity safely and reliably. Distran ultrasonic cameras are in use at numerous French nuclear power plants. Various departments such as Operations, Engineering, Reliability, HVAC, Automatisms, Testing & Monitoring, Taps & Valves (mechanics) use the devices as diagnostics tools.
As described above, Distran has helped EDF Dampierre-en-Burly avert a shutdown that would have cost 5 to 6 million euros per day. To safeguard the plant’s availability today and in the future, the Distran ultrasound camera is a central element of the periodic tests carried out to ensure that the installations are in good condition, which include:
- On-demand tests, led by Testing & Monitoring departments to look for air ingress on the condenser (vacuum: 1mbar of pressure loss is equivalent to 1MWh not produced).
- Weekly or bi-monthly tests by the Operations with air line tests and gas park inspections.
- MSR department tests to detect air and steam leaks.
- SPR department tests to detect CO2.
Diagnostics and monitoring: safeguarding the availability of France’s nuclear power plants fleet
As for all French nuclear power plants, EDF’s paramount objective in Dampierre-en-Burly is to produce low-carbon electricity safely and reliably. Distran ultrasonic cameras are in use at numerous French nuclear power plants. Various departments such as Operations, Engineering, Reliability, HVAS, Automatisms, Testing & Monitoring, Taps & Valves (mechanics) use the devices as diagnostics tools.
As described above, Distran has helped EDF Dampierre-en-Burly avert a shutdown that would have cost 5 to 6 million euros per day. To safeguard the plant’s availability today and in the future, the Distran ultrasound camera is a central element of the periodic tests carried out to ensure that the installations are in good condition, which include:
- On-demand tests, led by Testing & Monitoring departments to look for air ingress on the condenser (vacuum: 1mbar of pressure loss is equivalent to 1MWh not produced).
- Weekly or bi-monthly tests by the Operations with air line tests and gas park inspections.
- MSR department tests to detect air and steam leaks.
- SPR department tests to detect CO2.
“Using the DISTRAN camera for monitoring our networks and pressurized equipment,
allows us to increase both the nuclear safety and the availability of the Dampierre Nuclear Power Plant.”