09 Aug Chemical plant’s R&D team switches from soap spray to Distran’s camera, cutting inspections time by 3
Real World Stories: Chemical Industry
Chemical plant’s R&D team switches from soap spray to Distran’s camera, cutting inspections time by 3
With Ultra Pro X:
The maintenance team performs systematic leak inspections up to 3 times faster than traditional methods, allowing for comprehensive inspections every four months.
Operators quantify leaks in real-time, making it possible to calculate and report savings from fixing leaks, something not achievable with previous tools like soap spray.
Inspectors detect leaks from a distance, avoiding dangerous areas. It also significantly reduces the time needed for post-maintenance inspections, shortening overall downtime.
Real World Stories: Chemical Industry
Chemical plant’s R&D team switches from soap spray to Distran’s camera, cutting inspection time by 3
With Ultra Pro X:
The maintenance team performs systematic leak inspections up to 3 times faster than traditional methods, allowing for comprehensive inspections every four months.
Operators quantify leaks in real-time, making it possible to calculate and report savings from fixing leaks, something not achievable with previous tools like soap spray.
Inspectors detect leaks from a distance, avoiding dangerous areas. It also significantly reduces the time needed for post-maintenance inspections, shortening overall downtime.
A multinational industrial gas production company operating in more than 80 countries supplies oxygen, nitrogen, argon, hydrogen, and other specialty gases to medical, chemical, and electronics manufacturers.
There are two common situations where the company’s maintenance team find themselves inspecting for leaks:
1. Routine Maintenance
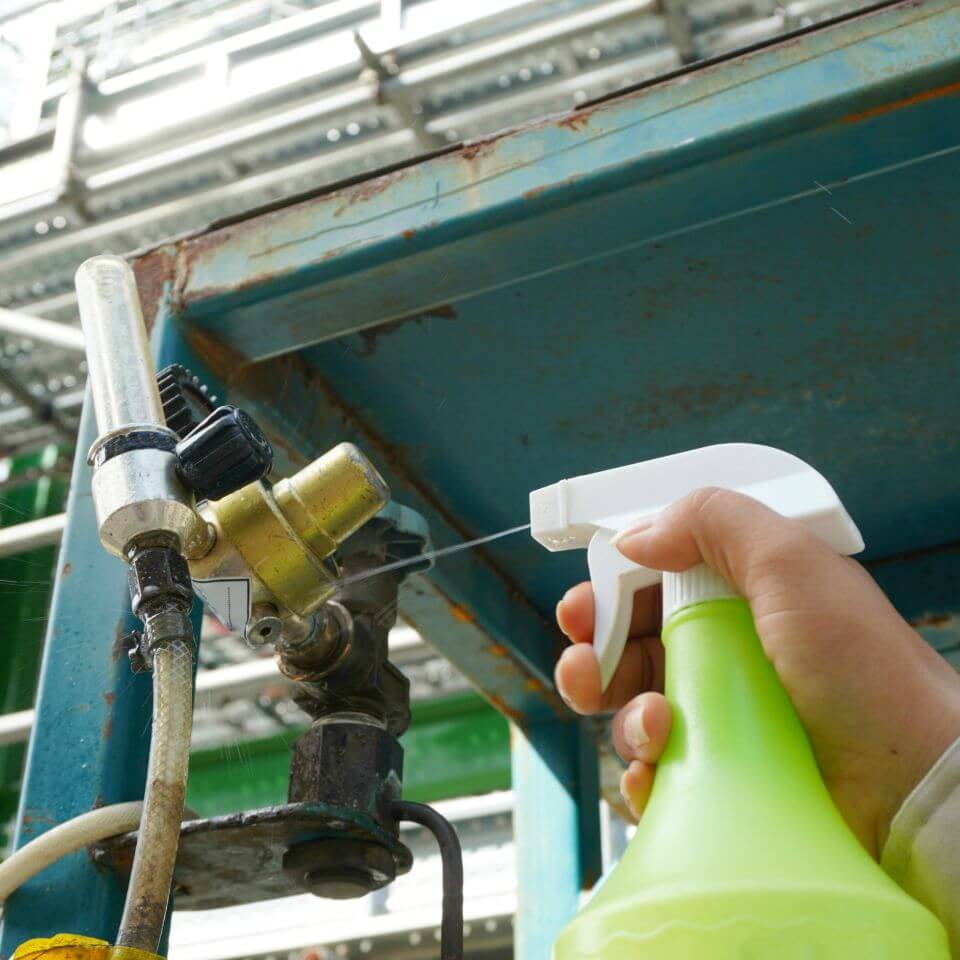
For routine maintenance, the operations team lacked a methodical approach to detecting gas leaks. Inspectors wanted to be more proactive and systematic, to find small leaks earlier, before damage is done to the equipment. But they were limited by the tools they had at hand: using their eyes, ears, scaffolding and soap spray. It was difficult and painstaking work. And they knew they were missing opportunities to improve efficiency.
Image: Using soap spray to detect gas leaks can be challenging.
1. Routine Maintenance
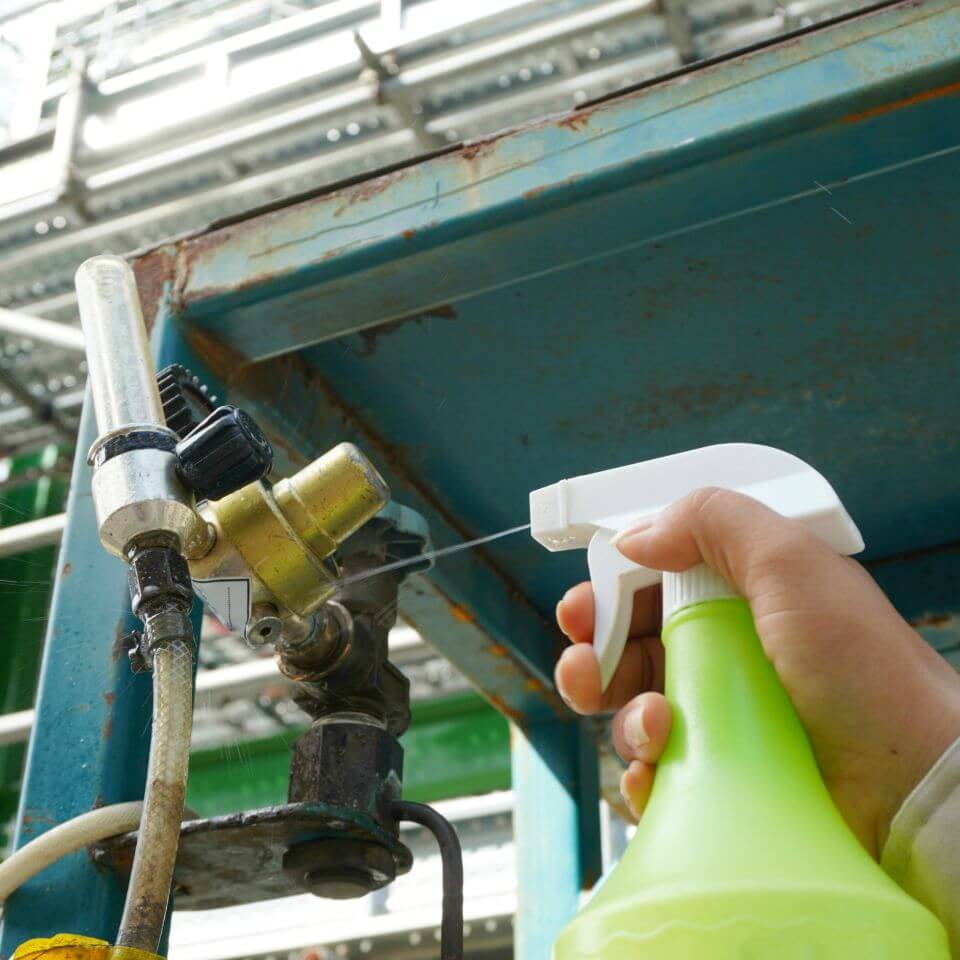
Image: Using soap spray to detect gas leaks can be challenging.
For routine maintenance, the operations team lacked a methodical approach to detecting gas leaks. Inspectors wanted to be more proactive and systematic, to find small leaks earlier, before damage is done to the equipment. But they were limited by the tools they had at hand: using their eyes, ears, scaffolding and soap spray. It was difficult and painstaking work. And they knew they were missing opportunities to improve efficiency.
2. Post Shutdown
After a plant was offline for repairs, commissioning, or outages, it was the norm to spend a day and a half to inspect for leaks. They manually checked flanges and joints each and every time a pipeline or compressor was opened.
The primary methods they previously deployed each had their drawbacks:
- Soap spray and scaffolding made gas leak inspections inefficient and imprecise.
- Ultrasound detection systems (the kind with wands and headsets) produced inconsistent results, because they depend heavily on an individual’s skills, and the environment. Some operators couldn’t detect differences in the signal because of the surrounding mechanical vibrations.
In an effort to innovate their way to efficiency and consistency, the company’s R&D team researched various solutions on the market and discovered the Ultra Pro acoustic camera.
As soon as they touched it, they were convinced.
The experience of using the device during demonstrations spoke for itself. No other device offered such a simple way to quantify leaks in real time, and quickly calculate the cost of a given leak.
Images: Detect leaks of any gas type or vacuum leaks
with a single tool.
2. Post Shutdown
Images: Detect leaks of any gas type or vacuum leaks with a single tool.
After a plant was offline for repairs, commissioning, or outages, it was the norm to spend a day and a half to inspect for leaks. They manually checked flanges and joints each and every time a pipeline or compressor was opened.
The primary methods they previously deployed each had their drawbacks:
- Soap spray and scaffolding made gas leak inspections inefficient and imprecise.
- Ultrasound detection systems (the kind with wands and headsets) produced inconsistent results, because they depend heavily on an individual’s skills, and the environment. Some operators couldn’t detect differences in the signal because of the surrounding mechanical vibrations.
In an effort to innovate their way to efficiency and consistency, the company’s R&D team researched various solutions on the market and discovered the Ultra Pro acoustic camera.
As soon as they touched it, they were convinced.
The experience of using the device during demonstrations spoke for itself. No other device offered such a simple way to quantify leaks in real time, and quickly calculate the cost of a given leak.
Success with the Ultra Pro:
Systematic Leak Inspection Program Expands Across Facilities
After successfully implementing a predictable, systematic leak inspection program across 20 facilities, enabled by the Ultra Pro device, more locations are following suit.
Here are the outcomes reported by the organization:
Success with the Ultra Pro:
Systematic Leak Inspection Program Expands Across Facilities
After successfully implementing a predictable, systematic leak inspection program across 20 facilities, enabled by the Ultra Pro device, more locations are following suit.
Here are the outcomes reported by the organization:
Surveys are easier
Stop spraying everywhere
The Ultra Pro allows the maintenance team to run proactive, methodical inspections less frequently, and post-maintenance inspections more rapidly. Instead of spraying everywhere, they locate the slightest of leaks much faster.
Surveys are easier
Stop spraying everywhere
The Ultra Pro allows the maintenance team to run proactive, methodical inspections less frequently, and post-maintenance inspections more rapidly. Instead of spraying everywhere, they locate the slightest of leaks much faster.
An entire site can be surveyed up to 3 times faster with the Ultra Pro than with soap spray. Comprehensive, proactive leak inspections are now performed every 4 months.
Maintenance is methodical
Be 3 times faster
Maintenance is methodical
Be 3 times faster
An entire site can be surveyed up to 3 times faster with the Ultra Pro than with soap spray. Comprehensive, proactive leak inspections are now performed every 4 months.
Leaks are quantifiable
Report on savings
Operators can quantify a leak, something they were never able to do with soap spray. Maintenance managers can report on savings generated as they fix more leaks.
Leaks are quantifiable
Report on savings
Operators can quantify a leak, something they were never able to do with soap spray. Maintenance managers can report on savings generated as they fix more leaks.
Inspectors can catch a leak sooner, while it is a smaller leak. The smallest steam leak can make an abrasion that’s impossible to fix once it passes a certain point. With the Ultra Pro, the team detects such small leaks very early, when there’s still time to re-tighten something, and prevent the whole system from coming down.
Shutdowns are preventable
Detect small leaks early
Shutdowns are preventable
Detect small leaks early
Inspectors can catch a leak sooner, while it is a smaller leak. The smallest steam leak can make an abrasion that’s impossible to fix once it passes a certain point. With the Ultra Pro, the team detects such small leaks very early, when there’s still time to re-tighten something, and prevent the whole system from coming down.
Downtime is shorter
Reduce leak inspection time
After a unit is offline, the leak inspection phase takes almost no time.
Post-maintenance, they inspect faster, resolve faster, and start faster.
Downtime is shorter
Reduce leak inspection time
After a unit is offline, the leak inspection phase takes almost no time.
Post-maintenance, they inspect faster, resolve faster, and start faster.
Maintenance managers found training to be very simple. For example, those who were unable to attend initial demonstrations were quickly brought up to speed by someone on the previous shift. There is no specialized training necessary to operate it proficiently, so anyone on site can step up and pitch in.
Anyone can pick it up
No specialized training necessary
Anyone can pick it up
No specialized training necessary
Maintenance managers found training to be very simple. For example, those who were unable to attend initial demonstrations were quickly brought up to speed by someone on the previous shift. There is no specialized training necessary to operate it proficiently, so anyone on site can step up and pitch in.
Workers are protected
Avoid contact with dangerous gases
When responding to an emergency, operators can stay clear of a potentially dangerous area and still precisely locate and quantify the leak from afar. Inspectors don’t have to get close to a hydrogen leak to locate it, which used to pose a risk to the safety of personnel. Plus, after shutdowns, inspectors no longer need to risk going up and down scaffolding again and again. They stay on the ground and turn on an axis to inspect a much greater radius from one spot.
Workers are protected
Avoid contact with dangerous gases
When responding to an emergency, operators can stay clear of a potentially dangerous area and still precisely locate and quantify the leak from afar. Inspectors don’t have to get close to a hydrogen leak to locate it, which used to pose a risk to the safety of personnel. Plus, after shutdowns, inspectors no longer need to risk going up and down scaffolding again and again. They stay on the ground and turn on an axis to inspect a much greater radius from one spot.