02 Jul How Bostik’s production team find leaks in unexpected areas quickly and efficiently
Bostik Success Story
How Bostik’s production team find leaks in unexpected areas quickly and efficiently
Highlights:
An elusive leak was found only with the Distran Ultra Pro.
8x faster inspection process vs traditional methods.
2/3rds fewer people involved vs traditional methods.

Bostik Success Story
How Bostik’s production team find leaks in unexpected areas quickly and efficiently
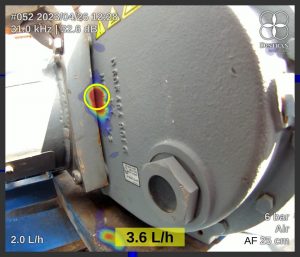
Highlights:
An elusive leak was found only with the Distran Ultra Pro.
8x faster inspection process vs traditional methods.
2/3rds fewer people involved vs traditional methods.
Bostik, a subsidiary of Arkema, is a global leader in adhesive solutions for the industrial, construction, and consumer markets. Operating in over 40 countries and employing 7,000 people, their product range includes adhesives, tapes, and specialty coatings.
The absence of leaks in production equipment is essential for guaranteeing product quality. Since 2022, Bostik’s production site in Ribécourt has used the Distran Ultra Pro acoustic camera to inspect its compressed air, nitrogen, and vacuum networks.
“The Ultra Pro allows us to detect the presence of leaks — and to validate the absence of leaks.
We save a ton of time by avoiding unnecessary dismantling.”
Thomas R.
Process Engineer, Bostik Ribécourt
The pre-production check

The production of polyester adhesives requires specific conditions. During polymerization, a high-vacuum environment with a pressure between 0.5 and 1.0 mbarA is necessary. Insufficient vacuum conditions can cause production delays and even product defects, such as a change in color.
So, before starting a new production run after a prolonged shutdown or maintenance, the team tests the system, checks for leaks, and ensures the vacuum conditions are within the necessary threshold.
After locating and repairing any vacuum leaks, production can begin.
Image: Polyester adhesives are used across industries, from construction to automotive.
The pre-production check

Image: Polyester adhesives are used across industries, from construction to automotive.
The production of polyester adhesives requires specific conditions. During polymerization, a high-vacuum environment with a pressure between 0.5 and 1.0 mbarA is necessary. Insufficient vacuum conditions can cause production delays and even product defects, such as a change in color.
So, before starting a new production run after a prolonged shutdown or maintenance, the team tests the system, checks for leaks, and ensures the vacuum conditions are within the necessary threshold.
After locating and repairing any vacuum leaks, production can begin.
An unexpected issue
In August 2023, the team was preparing to launch a system, but the pressure test failed. The vacuum level was 7 mbarA, indicating air was somehow entering the system.
Their initial approach was to use a single-microphone acoustic detector. This sort of device must be used in a targeted way, so they tested key points in the system where leaks are most likely to occur. This process yielded no results.
Image: Pressure test results – the measured pressure of 7 mbarA far exceeds the acceptable threshold of 1 mbarA.
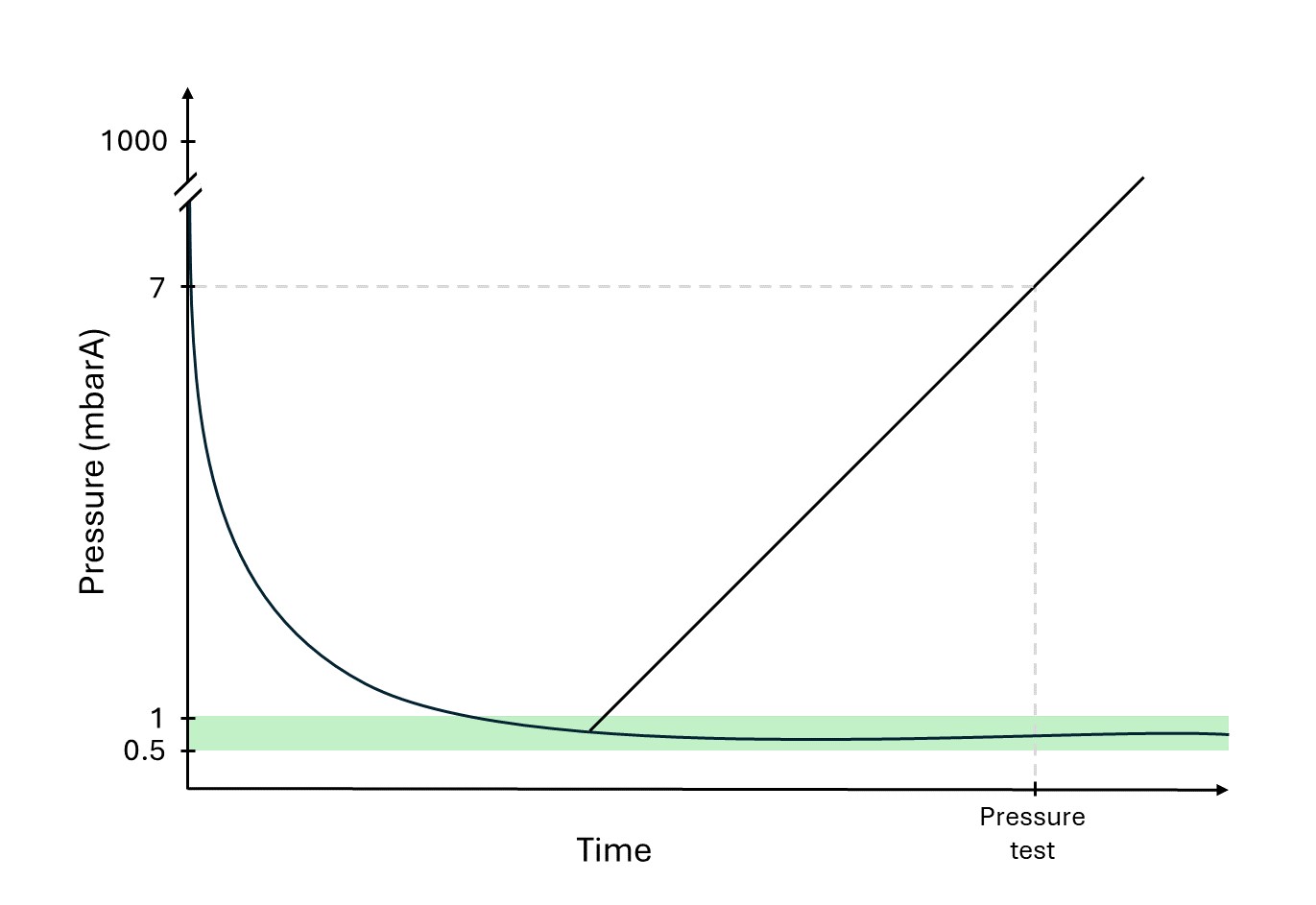
An unexpected issue
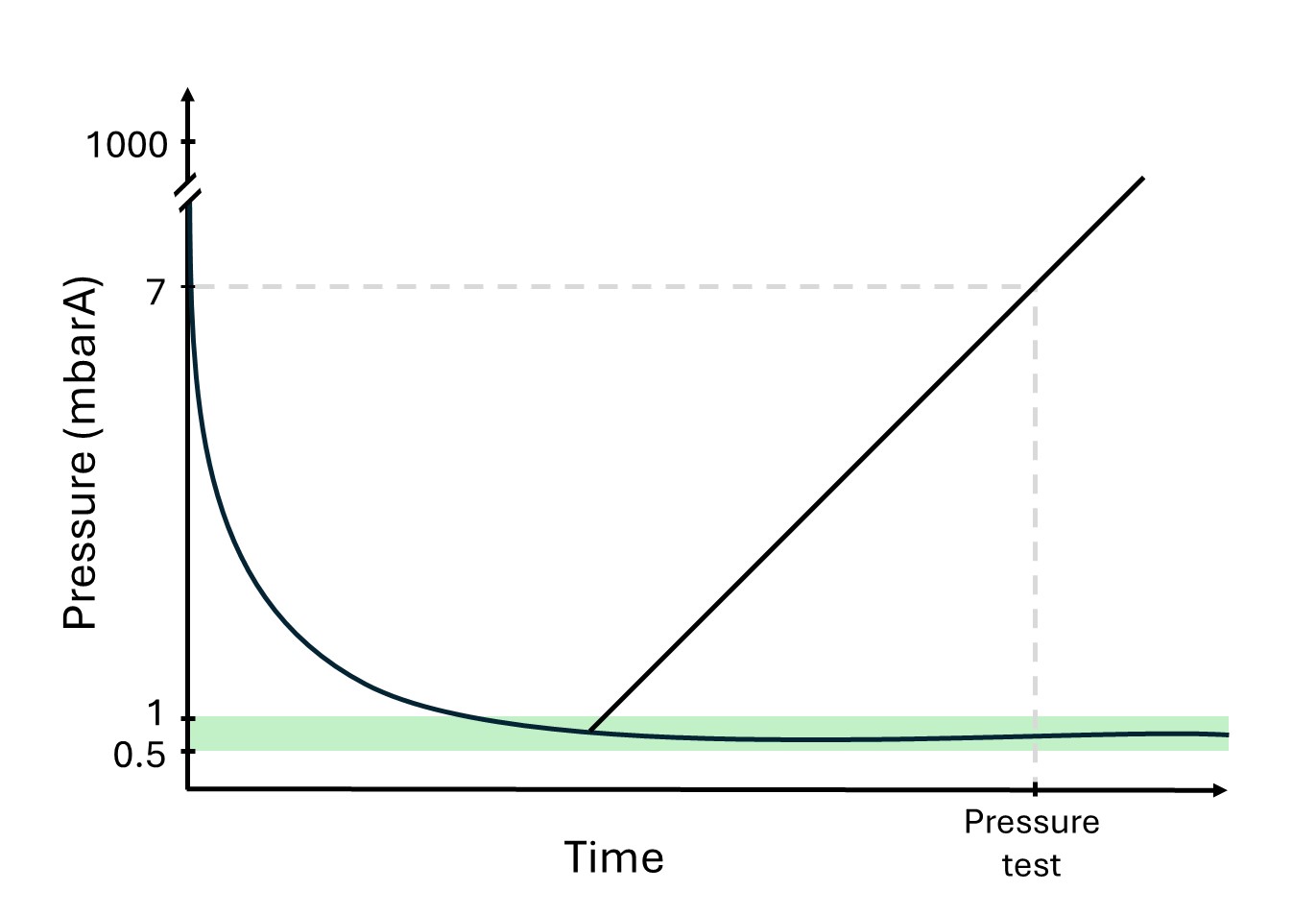
Image: Pressure test results – the measured pressure of 7 mbarA far exceeds the acceptable threshold of 1 mbarA.
In August 2023, the team was preparing to launch a system, but the pressure test failed. The vacuum level was 7 mbarA, indicating air was somehow entering the system.
Their initial approach was to use a single-microphone acoustic detector. This sort of device must be used in a targeted way, so they tested key points in the system where leaks are most likely to occur. This process yielded no results.
The last place to look
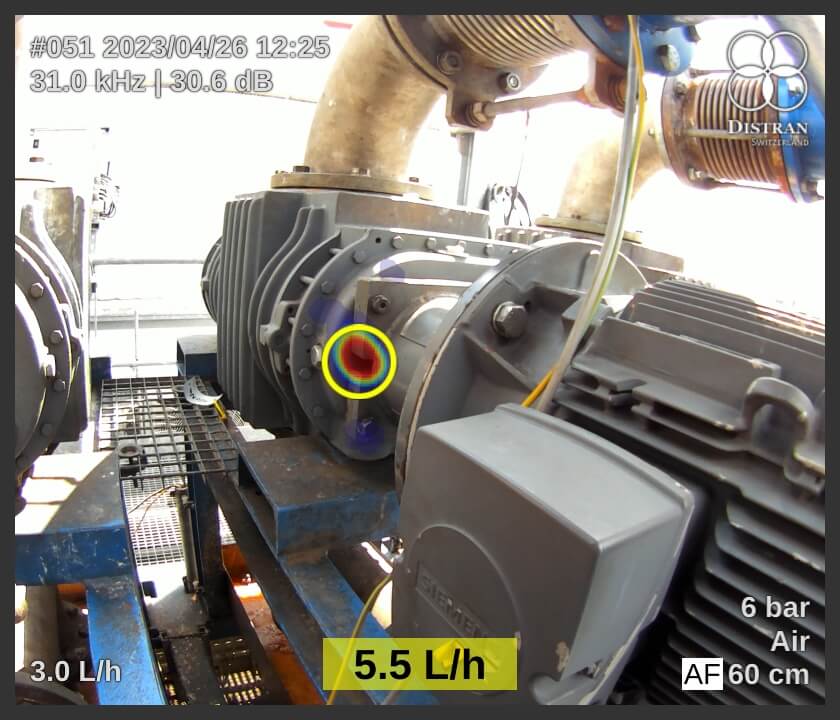
The Ultra Pro camera was then used across the full system, and the culprit was quickly identified: an unassuming vacuum pump coupling.
This was a surprise, as the inspection team had not considered this part a likely source of the problem and did not think it was worth checking.
Image: Vacuum leak detected with Ultra Pro ultrasonic camera on the vacuum pump coupling.
The last place to look
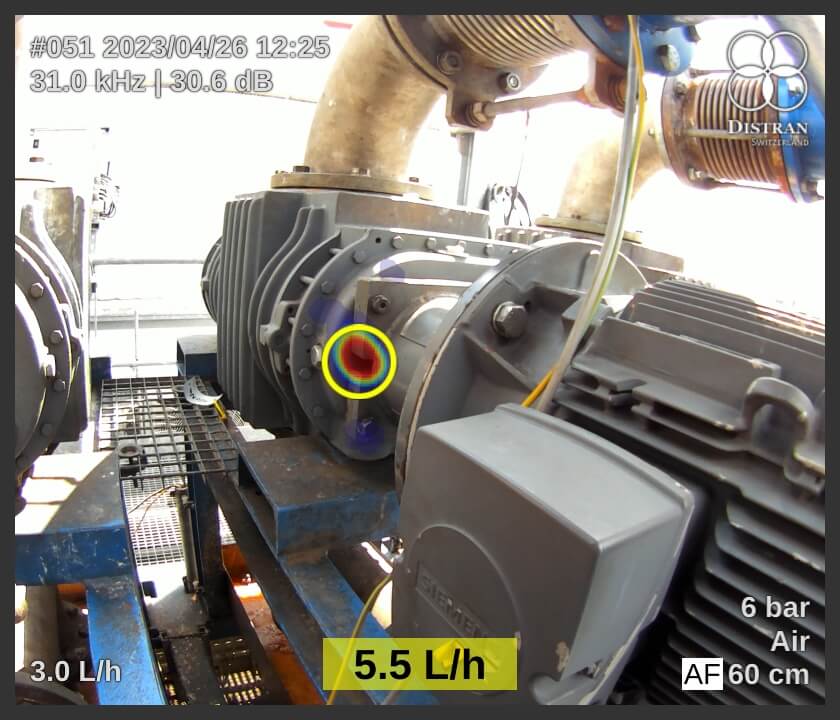
Image: Vacuum leak detected with Ultra Pro ultrasonic camera on the vacuum pump coupling.
The Ultra Pro camera was then used across the full system, and the culprit was quickly identified: an unassuming vacuum pump coupling.
This was a surprise, as the inspection team had not considered this part a likely source of the problem and did not think it was worth checking.
“A leak was clearly visible through the Ultra Pro camera at a vacuum pump coupling.
This leakage point would have gone unnoticed without this device.
No one expected it there.”
Thomas R.
Process Engineer, Bostik Ribécourt
Work better and faster
Traditional inspection methods typically take 8 to 10 hours. Using the Ultra Pro, Bostik reduced their testing process to just 1 to 2 hours: an 80-87% reduction.
Hundreds of potential leak sources were inspected by the maintenance team—and unanticipated leaks were discovered—in a fraction of the time.
1 hour vs.
8 hours
Reduced inspection time
Work better and faster
Traditional inspection methods typically take 8 to 10 hours. Using the Ultra Pro, Bostik reduced their testing process to just 1 to 2 hours: an 80-87% reduction.
Hundreds of potential leak sources were inspected by the maintenance team—and unanticipated leaks were discovered—in a fraction of the time.
1 hour vs.
8 hours
Reduced inspection time
Protect profit margins
Several 10k€
Reduced utilities
Postponing the start of production by even a day would have cost the company several tens of thousands of euros. Therefore, the speed with which leaks are detected and repaired is crucial for minimizing production line downtime and the associated financial losses.
By using the Distran camera, Bostik ensures continuous and efficient production, thereby reducing the company’s loss of earnings and protecting profit margins.
Protect profit margins
Postponing the start of production by even a day would have cost the company several tens of thousands of euros. Therefore, the speed with which leaks are detected and repaired is crucial for minimizing production line downtime and the associated financial losses.
By using the Distran camera, Bostik ensures continuous and efficient production, thereby reducing the company’s loss of earnings and protecting profit margins.
Several 10k€
Reduced utilities
Require less people
Inspections used to involve a minimum of three people. Using the Ultra Pro camera, a single person comprehensively inspects the same area.
Cutting the human resources spent on leak detection boosts the operational efficiency of this process, in Bostik’s case, by 67%.
+67%
Improved process efficiency
Require less people
Inspections used to involve a minimum of three people. Using the Ultra Pro camera, a single person comprehensively inspects the same area.
Cutting the human resources spent on leak detection boosts the operational efficiency of this process, in Bostik’s case, by 67%.
+67%
Improved process efficiency
With Ultra Pro, you will:

DETECT
LEAKS FASTER
Improve and accelerate leak diagnosis processes

FIND
UNEXPECTED LEAKS
Detect and pinpoint leaks in unexpected places

REDUCE
DOWNTIME
Confirm the absence of leaks and reduce disassemblies

GUARANTEE
PRODUCT QUALITY
Ensure reliability of installations and product compliance